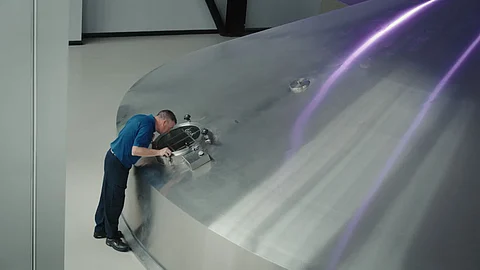
With the new generation of lautering technology, the GEA LAUTERSTAR 2.0, GEA significantly increases efficiency and quality in the brewhouse. In practical tests at breweries in Austria and the Netherlands, the system shows impressive results: Net lautering times were reduced to 70 minutes, and extraction efficiency increased to 98.7%. In a new project, the LAUTERSTAR 2.0 achieves up to 14 brews per day; while for another customer, upgrading an existing lauter tun boosted production from five to 8.5 brews per day.
Productivity in the brewhouse: the lauter tun as a bottleneck
In the brewhouse, the capacity of the lauter tun time and again proves to be a bottleneck for productivity and efficiency. Large international breweries in particular are looking for ways to unburden the lautering process: "Brewers have grown used to filtration taking a lot of time. We scrutinized these processes and found that we can lauter faster if the filter cake can be prevented from clogging. The GEA LAUTERSTAR 2.0 achieves a productivity increase of ten percent and an extract efficiency of 98.7%," explains Peter Sterk, Product Manager for Brewhouse Technology at GEA. Additionally, the new lauter tun is smaller, which results in material savings of ten percent.
Technical Innovations for faster lautering processes
To increase the efficiency of the LAUTERSTAR 2.0, GEA optimized the geometry and drainage points of the wort run-off cones. A larger distance between the false bottom and the lauter tun bottom ensures a more uniform wort flow and faster extraction. In addition, the new raking machine, equipped with special double-shoe knives, prevents compaction in the spent grain bed, thereby eliminating filter blockages. These compactions were previously responsible for two to three percent of wort losses.
Clear worts without solids, as produced in the GEA LAUTERSTAR 2.0, are particularly advantageous for energy-saving high-gravity brewing. With this method, higher concentrated worts are produced, which can be subsequently diluted. This allows breweries to increase their capacities without additional resources.
Optimized lautering thanks to GEA Multifunctional Lautering Management (MLM)
Depending on the raw material quality, net lautering times of 70 minutes can now be achieved while maintaining high lauter tun yields. For continuous optimization, the MLM software monitors the lautering process in real-time. It automatically compensates for fluctuations in raw material quality and relieves the brewmaster from manual interventions. This software makes dynamic adjustments to the lautering process, ensuring constant production times and consistently high extraction efficiency.
Upgrade of existing lauter tuns for cost efficiency
Another option is to upgrade existing lauter tuns to the LAUTERSTAR 2.0, which for many breweries makes economic sense. The investment pays for itself after just a few months, as demonstrated by the example of an Austrian brewery that was able to increase its production from five to 8.5 brews per day.
Click HERE to subscribe to our FREE Weekly Newsletter