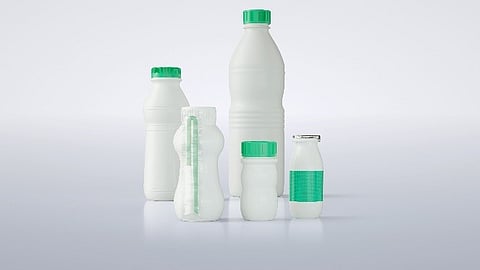
Liquids come in bottles: that is not only the case for drinks, but also for baby food and clinical nutrition, milk- and plant-based drinks, dairy products, and soups. Filling these sensitive products proves to be particularly challenging, as the process requires an aseptic environment. In addition, the packaging itself – the bottle sizes and materials – varies constantly. For food manufacturers and machine experts alike, it is quite the challenge to meet all these requirements. However, they can master this tricky, but not unrealistic balancing act by relying on versatile filling and sealing machines in aseptic executions.
Kefir, soups, baby food and clinical nutrition – the list of bottled foods is long. Nutrition trends such as liquid meals, which promise a daily ration of calories, but also the requirements of certain consumer groups favor this form of marketing. In some cases, the products are an absolute necessity: consumers in a weakened state such as infants or patients need proteins and minerals in dissolved form as they cannot consume them otherwise or only with great difficulty. But regardless of whether it is a short-lived hype or a vital form of nutrition, in both cases, manufacturers are faced with the pressing question of how to fill liquid products safely, in large quantities and in different bottle formats and materials.
An abundance of packaging formats and materials
After all, not all bottles are the same: not glass bottles, as used in beverage filling, but blown or injection-molded and pre-sterilized plastic bottles protect liquid foods from external influences. Manufacturers rely on HDPE as well as PET and PP. Due to its particularly high barrier properties, HDPE is primarily used for highly sensitive products such as clinical and infant formula. The easily recyclable PET options are the bottles of choice for everyday products such as milk- or plant-based drinks, dairy products, and soups.
PET bottles are part of many food manufacturers' portfolios for sustainability reasons, if product and production requirements allow for it. PET in particular closes a crucial gap in the circular economy due to its material properties: at the end of their life cycle, PET bottles are increasingly shredded instead of being disposed of – and thus form important regranulate for marketable PET bottles[1]. PET bottles and corresponding recycling technologies are thus helping to achieve the targets set out in EU regulations[2], according to which beverage bottles should consist of 30 percent recycled material by 2030.
Not only the material, but also the formats of the bottles vary and prove to be as useful as they are challenging during filling. Production volumes of several thousand units per hour are quite common. Manufacturers can only achieve these high output rates if their production runs as smoothly as possible. If more than one bottle format or material is to be filled and sealed efficiently on the same line, there is no way around fast changeovers.
Bottle transport is key
One process step is proving to be crucial: transporting the decontaminated, upright bottles from the machine infeed to the carrier plates. One possible option for bottle transportation in the food industry are machines that grip bottles at the bottom. Neck handling simply reverses the principle and ensures particularly effective transportation. Instead of at the base, the machine grips bottles at the neck. As the neck, unlike the base, rarely varies in diameter, manufacturers can process several formats with minimal adjustments. If changeovers are needed, they are equally quick and minimal.
Ampack has also made use of neck handling and developed it further for the new FBL filling and sealing machine. With this innovation, the Königsbrunn-based company is expanding its portfolio for flexible and aseptic filling of liquid food products. "With the FBL, we offer manufacturing companies the option of filling HDPE, PET, and PP bottles on one machine – and thus of meeting the demands of a dynamic market environment," explains Oguz Karcier, Product Manager at Ampack, a Syntegon company. Current packaging standards can change quickly: "If advanced PET becomes suitable for clinical nutrition in the future, manufacturers will not need a separate machine. The FBL stands for flexible transport – and equally versatile sterilization," adds Karcier.
No chance for germs
Here is why: Manufacturers must achieve high disinfection rates when filling highly sensitive products such as infant formula, liquid patient meals or certain dairy products to ensure maximum product protection and a long shelf life both inside and outside the cold chain. The FBL meets the highest safety requirements in this respect, as aseptic filling is one of Ampack's core competencies. "All bottle materials can be effectively decontaminated thanks to the FBL's new sterilization system," continues Karcier. This versatility is needed for good reason. PET, for example, is more temperature-sensitive than other materials and is more prone to absorbing the hydrogen peroxide (H2O2) used for sterilization. Thanks to precise temperature control, the FBL can handle each of the materials mentioned and ensures reliable sterilization.
However, the FBL takes product safety into account on more than one level: "Our innovative hygiene concept complies with international standards such as 3-A and includes a double chamber system that separates the mechanical and filling areas," continues Karcier. The Ampack machine has an additional sterile chamber to minimize the risk of food contamination. The mechanical parts are located in a separate area. As a result, the filling process becomes flexible and abso – for a variety of formats, but also for a variety of consumers.
[1] https://www.recyclingmagazin.de/2020/06/08/pet-recycling-auf-dem-weg-zur-kreislaufwirtschaft/
[2] Vgl. https://environment.ec.europa.eu/topics/plastics/single-use-plastics_en?prefLang=de
Click HERE to subscribe to our FREE Weekly Newsletter