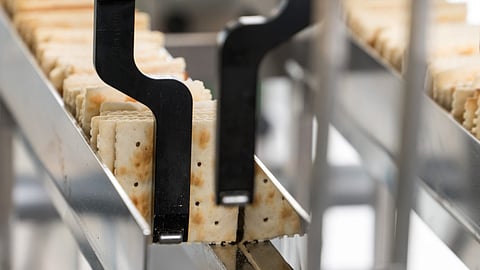
Working in close cooperation with customers is a top priority for Syntegon Technology. Two virtual events at the Swiss site in Beringen from 25 February to 3 March facilitated the exchange during the pandemic. The events focused on innovative packaging systems for bar production and Syntegon’s expertise in safe and reliable cracker handling. “We not only want to show our customers our future-proof solutions; we also would like to foster a dialog,” explains Bruno Oberle, vice president of product group horizontal packaging systems. The online event concept included live machine demonstrations and expert discussions on trending topics in the food industry, including sustainability, flexibility, and hygienic design. “Small and exclusive event sessions offered customers the opportunity to ask questions, address their needs and challenges, and discuss them with our experts.”
Live from the shop floor to the (home) desk
The exclusive “Chocolate & Bar Show” started on 25 and 26 February, where Syntegon presented a system for primary and secondary packaging of bars. After the bars have been formed, dried, and cut, the new Sigpack DCIE discharge station gently arranges them crosswise and distributes the bars onto the packaging leg.
A 3D quality check is performed to remove products with poor quality from the packaging process. In the next step, the innovative FIT product feeder transports the bars reliably and efficiently thanks to intelligent linear motor technology, a solution that has already been successfully implemented 100 times in the market. The bars are cold-sealed and wrapped in paper using the paper-ON-form module in the Sigpack HRM flow-wrapping machine. The primary packaged bars are then put into the correct position via the new PFI infeed and are fed into the integrated Sigpack TTM2 top load cartoner.
Reliable packaging of cookies and crackers
The “Cookie & Cracker Show” on 2 and 3 March presented a flexible high-speed system for the reliable handling and packaging of crackers. The solution features particularly gentle handling and a hygienic design with a small footprint. Thanks to the flexible configuration, different shapes can also be optimally processed on the line. Crackers are grouped at speeds of up to 400 slugs in a minute. The HCS flow-wrapping machine with fully automated new AHS heat-sealing technology enables extended sealing times and ensures tighter packages for a longer product shelf life. Customers have the option to switch between mono and multilayer films. Moreover, the system can be switched from short to long slugs within ten minutes, providing maximum flexibility.
Virtual exchange on trending topics
Syntegon also uses the virtual event for an active exchange with customers. The focus of the event was on current trends and challenges. “These include, for example, technologies such as linear drive, 3D vision inspection, and sustainable solutions such as paper or mono-material packaging,” says Oberle. “We want to understand our customers and their needs thoroughly. Last year we began running digital factory acceptance tests, which were very well received. We want to build on this and further intensify global partnerships despite limited travel opportunities.”