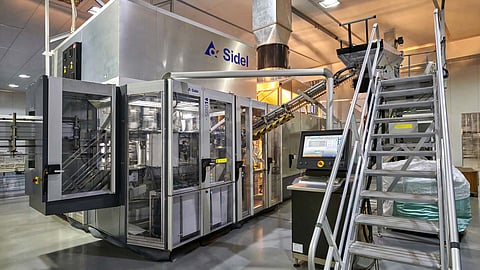
Founded in 1970, Willowton is a family-owned business in Pietermaritzburg, South Africa. With its innovative approach and hands-on attitude, Willowton has established itself as one of Africa’s leading oilseed processors and edible oil packers. It is the top edible oil manufacturer in South Africa, too, and it owns the country’s leading sunflower oil brand, Sunfoil. Thanks to its in-house oil refinery that has been in operation for over four decades, this regional powerhouse also produces edible oil for retail brands.
To increase its yearly production volumes and differentiate its Sunfoil brand from traditional edible oil brands with generic container shapes, Willowton decided to partner with Sidel to produce its PET containers in-house. To achieve this, the company acquired two Sidel EvoBLOW standalone blowers and relied on Sidel’s packaging design skills and experience to help it develop customized family bottle shapes.
Superior production flexibility
One of the many benefits these new standalone blowers offer is a more independent bottle production set-up. The equipment also enables efficient production planning and reduces warehouse space. The SBO 16 EvoBLOW produces a 2 L format while the SBO 10 EvoBLOW produces all bottle formats up to 1 L. As the latter manages various bottle formats, Willowton also chose to install a mold Bottle Switch system to conduct ultrarapid bottle changeovers. “This easy way to adapt our oil production to the fast-moving market demands contribute to a great production flexibility,” comments Faisal Modi, operations manager at Willowton. This system is based on repeatable, tool-free operations that mean the operator spends only 30 seconds per cavity, increasing production flexibility, equipment availability, and production uptime. Both machines can operate at an efficiency level of 99.5% regardless of the End-of-Line performance, thanks to the production buffer created by the storage silos located on the lines. “With those two blowers, we already increased our yearly production volume by 50%, and we are ready to handle any future additional demand as well,” explains Faisal Modi. To meet consumer expectations regarding superior hygiene standards, the two Sidel blowers have been equipped with different options to ensure production integrity. These include preform dedusting, air filtration, air recovery, and automatic centralized greasing.
New, distinctive family bottle design with a drop logo
Starting from a series of modern designs that were developed using bottle drafts and digital mock-ups, technical designs, and prototypes with 3D printed models, the new elegant, cylindrical Sunfoil silhouette with a drop logo engraved on the bottle shoulders was created. This bottle is more practical as its belt-inspired design and reduced diameter make it easier to handle. The new shape has been applied to different family bottle sizes, including 375 ml, 500 ml, 750 ml, and 2 L (a rectangular bottle). The latter was the most challenging format because blowing a rectangular bottle without any specific preferential heating blowing process affects the structural rigidity of the container. Sidel, therefore, conducted various packaging evaluation and qualification tests on the 2 L bottle, including Finite Element Analysis (FEA) and feasibility trials to improve its strength and performance across supply chain simulations. The bottles are equipped with push fitting or screw closures.
“Implementing this project went particularly smoothly, and we are all really happy with the result,” commented Modi. To make the most of the blowers’ operation, Sidel also organized training courses for the Willowton operators before and after the equipment validation process. They were performed by Sidel local technical experts on-site and empowered the Willowton team, enhancing their skills while reinforcing trust between Sidel and Willowton.