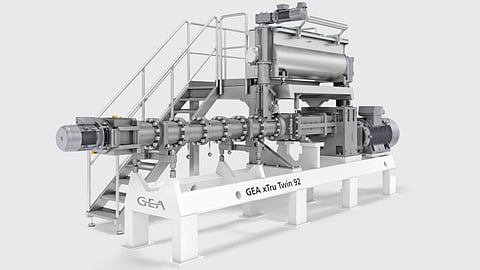
The new top-of-the-range machine is equipped with an advanced profile; powered screws provide users up to 40% increased capacity with the same efficiency, quality and footprint as previous models. Additionally, this high-capacity technology can be applied to the other GEA xTru Twin extruders models too – models 70/92/112 – and retrofitted to older machines to increase their capacity without changing floorplan of the factory.
The GEA xTru Twin extruders offer the flexibility to produce a wide range of products including: cereal-based snack pellets die-cut, 2D, 3D, multilayers, square shape, punched and direct expanded; breakfast cereals; dry pet food; and any other extruded food product. The latest xTru Twin 140 has a production capacity of over 3 tons of pellets and 10 tons of pet food kibbles an hour.
More capacity but same footprint ... same machine!
To achieve the additional capacity, GEA engineers have used their experience and know-how to increase the cross-sectional area, rotation speed and pitch of the screws on the new machines while maintaining the extruder footprint and screw length. This also allows customers to upgrade existing machines without buying a new one or changing the plant layout.
Increased quality, hygiene and safety
Other key features of the GEA xTru Twin range include: A high-speed premixer for perfectly hydrating flour; a large, curved mixing vessel that facilitates good water absorption and adhering to the requisite hygiene standards; a vertical forced feeding screw to control the dough's movement into the cooking screw; a powerful, variable-speed motor with a safety clutch; a high-torque, double cascade gearbox that ensures excellent power reserves and safety. With its co-rotating, fully intermeshing twin screws, a modular barrel assists in properly cooking cereal-based dough.
Driven by customer demand
GEA embarked on the process of developing the new technology in response to customers' requests and the market's need for a single, high-capacity machine capable of producing a wide range of innovative food shapes. Thanks to this new technology's flexibility, customers can develop new products and get them to market quickly and profitably.