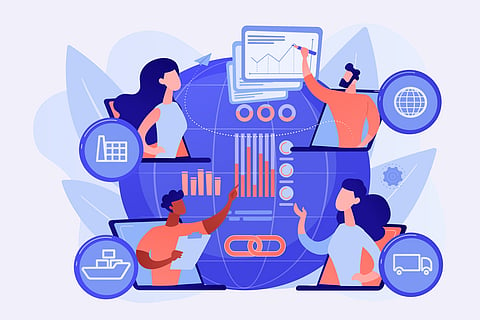
India's food-tech ecosystem is as complex and diverse as the country's cuisines. Supply chain management in this complex sector is genuinely unique, with numerous players competing and coexisting, ranging from Kirana stores (mom and pop shops) to supermarkets, mega marts, restaurants, and finally, online players entering the picture. With such a large ecosystem comes enormous potential as well as unique challenges to the Indian food industry. Some of the most persistent challenges stem from complexities or outdated inventory management, storage space, and stock management infrastructure.
Businesses have been forced to deal with supply chain disruptions and decreased sales due to the Covid-19 pandemic, which has hit the food industry especially hard. Supply planning, distribution, and customer acquisition were already difficult before the pandemic, and the frequent lockdowns have further worsened the situation.
On the other hand, the pandemic has catalyzed digital transformation, paving the way for analytics and automation in a traditionally relied-on manual operations field. Food players have recognized the importance of incorporating Artificial Intelligence (AI) into their business processes to address challenges, particularly those related to replenishment planning and managing SLOB (Slow Moving and Obsolete Inventory), which are critical to maintaining a robust supply chain food-tech space.
Replenishment strategies for the post-pandemic world
Maintaining inventory levels is one of the most challenging aspects of the supply chain, directly impacting maintaining a high level of consumer satisfaction. Navigating the fine line between overstock and stockout, businesses must avoid forecasting errors and gain visibility into any manufacturing constraints as well as real-time market data (or real-time demand). According to Harvard Business Review research, 72% of stockouts are caused by retailers purchasing too little or too late, making inaccurate demand forecasts, or otherwise mismanaging inventories.
The ultimate goal of a smart replenishment plan is to always fulfill demand without overstocking and losing money. The right focus on ensuring successful implementation of processes like ABC Analysis (A- High-Profit margin, well selling; B- Mid-range items; C- Low-profit margin), determine accurate lead times, replenish from within the business, reorder point strategy by monitoring the inventory in real-time and the right demand strategy to plan replenishment based on demand can help achieve this goal.
A good replenishment strategy is based on optimizing three fundamental functions - fluctuating forecasts due to market volatility, storage space, transportation, and visibility. Businesses will significantly reduce stockouts and overstock by utilizing real-time data and the appropriate demand forecasting solutions.
Identifying and avoiding obsolete inventory
In a time-sensitive market like food, identifying and eliminating SLOB or obsolete inventory is critical. Obsolete inventory can severely impact a company's bottom line. Inventory charges consume a sizable portion of a company's working capital.
Inventory management requires accurate, granular forecasting as well as visibility into inventory trends. When there is an excess of inventory, the costs of storage, transportation, and other factors rise. These patterns indicate potential issues that could result in wastage at all levels of the supply chain and, ultimately, SLOB.
Poor or very aggressive forecasting, unoptimized replenishment and safety stock, and unoptimized redistribution are the top three causes of SLOB inventory. Sorting this out would aid in streamlining the supply chain and preventing obsolescence. There are methods to resolve this.
So, how can using the right technology or tool be a game-changer for a food business owner or player to tackle obsolete inventory?
Accurate new product forecasting
Look for solutions using machine learning algorithms to analyze previous or similar product launches and execute scenario modeling to forecast numerous scenarios. Users will be able to generate the most accurate forecasts for any new product launches at all granularities.
Optimized replenishment
When dealing with dynamic inventory norms and propensity analysis, invest in solutions that allow real-time forecasts of the right quantity of SKUs to restock at the needed location. This enables you to prevent excess stock accumulation by adjusting safety stock levels based on demand forecasts, seasonality variances, trends, supplier lead times, and a product's place in its life cycle.
A little overly optimistic projection can result in SLOB losses of millions of dollars. It is critical to take steps to prevent slow-moving merchandise from becoming obsolete.
The food space and supply chain automation are at the cusp of transformation in India. Brands that have already adopted AI and machine learning to optimize their supply chains will stay ahead of the curve and better manage demand forecasting, replenishments and eliminate obsolete inventory. Therefore, the question an individual within the food business should be asking is "Am I using best-in-class technology to manage my business?" If the answer is no, you should reconsider your AI business strategy.
Rahul Vishwakarma, co-founder and chief executive officer, Mate Labs
Photo attribution -<a href='https://www.freepik.com/vectors/cartoon'>Cartoon vector created by vectorjuice - www.freepik.com</a>